Your privacy settings
We and our 1 partners store and/or access information on a device, such as unique IDs in cookies to process personal data. You may accept or manage your choices by selecting accept or reject all, or at any time in the privacy policy page. These choices will be signalled to our partners and will not affect browsing data.
We and our partners process data to
Use precise geolocation data. Actively scan device characteristics for identification. Store and/or access information on a device. Personalised advertising and content, advertising and content measurement, audience research and services development. List of vendors.
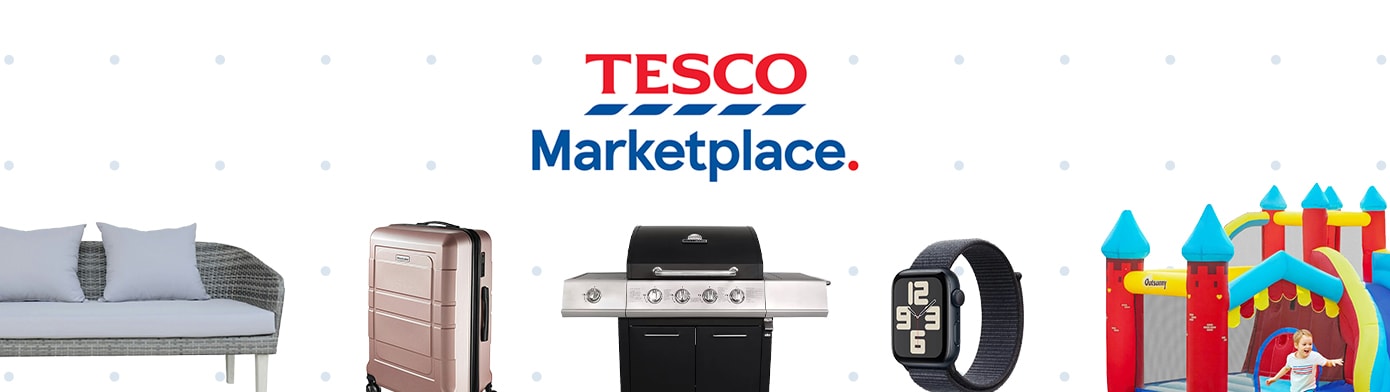
Deals | Homeware | TV and audio | Garden and outdoor | Kitchen gadgets | Toys | Baby and toddler | Sport and leisure | Pet | FAQs
Direct from Tesco sellers
Your basket just got a whole lot bigger. Bag weekly offers and big savings, all in one place. Keep popping back - there's always a deal waiting.
Popular and trending
Not sure what to choose? Take a peek at what everyone else is loving right now.
Fancy something a little different?
Did you know we sell fancy dress? And snazzy bubble wands, summerhouses, even 41-bottle wine coolers? Check out some of our latest unexpected finds.
Shop by department
Curious about our ever-growing range? Browse our online aisles and collect Clubcard points with every purchase.
All Marketplace sellers
Check out our growing list of sellers and find their contact details now
Frequently asked questions
Got questions about our sellers? We've got the answers.
Online Marketplace at Tesco
Step into the world of our online Marketplace where you'll find the latest kitchen electronics to inspire your cooking and stylish garden furniture to refresh your outdoor space. Wrap up in our cosy bedding and blankets during nippy evenings, and set the stage for memorable family meals with our chic dining sets. For little adventurers, we have a treasure trove of children's toys to fuel imagination and play. Upgrade your entertainment with our selection of top-notch TVs, and explore our beauty aisle for your self-care essentials. Don't forget to gear up with our sport and fitness offerings, ready to support your active lifestyle. The Tesco Marketplace is your destination for quality and variety, from the comfort of home.
Basket
Groceries
Reserve a slot for either home delivery or collection
Grocery basket empty
Products you add to your basket will appear here